In practice, pharma designs, develops, and controls processes via the use of appropriate and effective online and offline tools. Most processes are sufficiently designed to operate without PAT. However, it should be understood that this is a net reduction of labor. A technical strategy should be developed for accomplishing the systems integration that will be required. The use of well-designed and robust processes and analytical testing strategies (which include analyses of incoming materials, in-process materials, isolated process intermediates, drug substances, and finished drug product) enables us to confidently ensure product quality. 2022Gartner, Inc. and/or its affiliates. If the PAT method is being introduced to a process that is currently producing an approved product, the regulatory department will need to make submissions to have the change in the process approved. In a PAT approach, for example, the analysis technique is interfaced with the reactor for real-time analysis. This could include how many spectral readings to take, which wavelengths to read, and whether to average spectral readings over several readings. Supporting and maintaining PAT instruments will require additional workload and skills from the instrument technicians. In traditional product development, these lines interact, but largely function with a level of independence. In the traditional offline approach, one is essentially taking several snapshots, at the same time, from samples obtained from different locations in the blender. Implementing PAT-based measurement and control requires specialized tools. Please enter an email address in the field above. in biochemistry from Beloit College. John D. Orr, Ph.D., managing advisor with Rondaxe Pharma, LLC, has 25 years of pharmaceutical chemistry, manufacturing, and controls (CMC) experience. Faster product release: It is possible that PAT measurements may eliminate some post production testing and allow material to flow through the process faster. Visit our ISA Global Cybersecurity Alliance (ISAGCA) blog here. He has a BS in chemical engineering from the University of Texas at Austin and 35 years of experience in process engineering, development, and automation. It could also be necessary to coordinate when the reading should be taken with the process. These groups all have different roles and deliverables, and often are within different organizational lines. Interested in reading about automation cybersecurity? Manufacturers are moving away from this approach toward a quality-by-design approach by combining a higher level of process understanding with more sophisticated real-time monitoring and control. Welcome to the official blog of the International Society of Automation (ISA). July 24 There are a variety of challenges that must be addressed. Method specificity is obtained via the specific frequencies selected (Figure 2).
Get the latest articles from Pharmaceutical Online delivered to your inbox. Process development: Ideally, PAT should be part of the quality-by-design strategy, and all new processes should be developed to leverage available PAT technologies. and Ph.D.), and performed post-doctoral studies in molecular biology at The Noble Foundation. All rights reserved. PAT implementation at Hovione is under the responsibility of a global support group established over 15 years ago, serving both development and commercial stages across all Hovione sites.
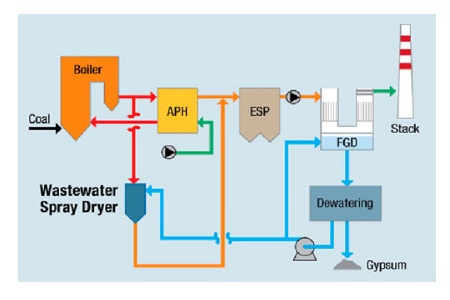
This results in a delay between process sampling and when the results are available. An appropriate level of expertise is needed in house even to provide oversight of contractors. This results in a resource (human and financial)-intensive effort. In the PAT approach, one is essentially recording a movie, but only from one spot in the blender, with the assumption that the observations made there are representative of the entire blender. Get more pharma manufacturing insight with our FREE newsletter, validated manufacturing processes with well-defined operating ranges, National Institute for Bioprocessing Research & Training (NIBRT), 2017 Land O'Lakes Pharmaceutical Analysis Conference. As a common example, ibuprofen reduces inflammation and pain. Credit for improved quality may be taken as reduced cost or increased revenues, depending on whether or not the facility is limited in capacity. Note: Chemometrics is the chemical discipline that uses mathematical and statistical methods to design or select optimal procedures and experiments, and to provide maximum chemical information by analyzing chemical data. The implementation of PAT requires changes to how processes are developed, analyzed, and produced. Like most innovations, big pharma has led the way, because it has significant resources. The pharmaceutical manufacturing industry has had to work within the constraints of regulation for many decades, which has inhibited a culture of continuous process improvement and caused less than optimal manufacturing practices. The Food and Drug Administration (FDA) initiative for current good manufacturing practices (CGMPs) for the twenty-first century has encouraged the adaption of new technologies to improve manufacturing. During process risk assessments, high-risk areas are identified and appropriate controls are developed and implemented, some of which may include PAT measurements and feedback loops to control the process to produce a product with the target quality attributes. Specialized instruments: PAT instruments are very different than traditional temperature, pressure, and flow devices. It should be viewed as an overall system, including instruments, modeling software, data management, process control, and integration of the components. and Once a process has been validated and approved, it is fixed until a change is accepted via a Change Being Effected notification (CBE) or a supplement requiring prior approval (PAS). In traditional approaches, samples are periodically taken from the reactor, quenched, if need be, and brought to the testing lab. The challenges of the PAT approach include the selection of the appropriate PAT technique and functional groups for reaction monitoring, spectral interferences resulting from components and process conditions, and the need for more sophisticated data analyses to visualize and interpret the results. Gartner Terms of Use Lustri has worked for Emersons life sciences industry group for 15 years in a variety of capacities. With a drug substance, for example, reactants A and B are combined to form product C. The process is monitored for the disappearance of reactants A and B, and the formation of product C and potential byproducts. In such a paradigm, PAT implementation suffers. Expert insights and strategies to address your priorities and solve your most pressing challenges. | George earned doctorate in chemistry from Missouri University of Science and Technology and a B.S. Analytical methods are not commonly critiqued during regulatory market application review. Improved quality could also result in better yield. The ongoing debate over the use of PAT versus traditional analytical tools and controls may be one of semantics. The limitation with the PAT approach, though, is the assumption that the sample in contact with the PAT spectrometer is representative of the entire blender contents. For those processes that would benefit from real-time monitoring, often the PAT measurement is correlated to a process parameter that can be routinely monitored with a low-technology (univariate) probe and sensor (e.g., pH, temperature, pressure, turbidity). Product Not Found. By clicking the "Continue" button, you are agreeing to the Those now embarking on implementing PAT can take advantage of the lessons learned and best practices that have been developed to date. These are listed in table 1. PAT method management: Similarly to the models, the PAT methods must be maintained under revision control. When this is baked into the process development process, the effort for regulatory approval is simply part of the standard regulatory approval process for a new drug. Please refine your filters to display data. The final piece of the puzzle is a PAT management software platform that is needed to manage data and integrate the PAT instrument with other data and control solutions. A version of this article also was published at InTech magazine. Using PAT to detect the processing end point can reduce the cycle time. This is done by taking measurements, during processing, of Critical Quality Attributes (CQA) of raw and in-process materials and processes to ensure product quality. Please remove or try a different part number. The multivariate model that defines the boundaries where the process can operate is known as thedesign space. Additional requirements include the scientists having the requisite knowledge, expertise, and instrumentation for the selected technique. Because there will be challenges, the sponsoring executive must be convinced of the benefits. 9:00 a.m. CDT. The appearance, disappearance, or change of bands at representative wavenumbers allows for monitoring of a reaction. Chemometric models: The development of models for calibrating instruments with spectral data output requires specialized skill sets and experience.
The limitations include fewer samples, longer analysis times, reactor perturbations from sampling, and the potential for the sample no longer being representative of the reactor mixture. As defined by the United States Food and Drug Administration is a system for designing, analyzing, and controlling pharmaceutical manufacturing processes. The following represent the primary tool kit for implementing PAT-based control: Analytical instruments used for PAT measurements are typically advanced analytical instruments using the light spectrum to characterize a quality measurement. To help understand the apparent pedestrian uptake in PAT, it is helpful to understand pharmaceutical processes and analyses. Or, it may be decided the best place to start is a high-volume product in production that will deliver lots of benefit. In the next article in this three-part series, the authors discuss the application of spectroscopic measurements in lieu of more traditional analyses (e.g., chromatography, Karl Fischer) to provide familiarity with the tools, process, and typical samples.