This practice will allow you to streamline and accelerate data collection and management, model development, model validation, and model deployment. As this depends on obtaining quality data, the first step is to. Temperature variations are useful for assessing the condition of motors and mechanical and electrical components, the building insulation, and even the condition of solar panels. Predictive maintenance is one of the most important parts of the maintenance process. Among the predictive maintenance techniques used in the industry are: Thermographic analysis can also be applied to several types of equipment to detect wear, rusting, delaminations, and disconnections that might go unnoticed to the naked eye. A study by the United States Department of Energy in 2010, when installing sensors was even more expensive than now, points to 25-30% reductions in maintenance costs, 35-45% less downtime, and 70-75% fewer breakdowns. Finally, you need to train and test your predictive maintenance machine learning model using samples from your data set. Predictive maintenance achieves this by predicting when maintenance is required, allowing the maintenance frequency to be as low as possible for an asset. Accumulating data about your assets is of no use if you dont know how to exploit them. Heres My Love Story, From Concepts to Creations: Making Dreams a Reality, Announcing our $4.5 million seed round led by CRV, Artificial Intelligence Call CentersComing To A Future Near You, Machine Learning in Insurance: Real-World Applications, Benefits of a No-Code AI Platform for ML Infrastructure and ML Ops, AI Act: A Risk-Based Policy Approach for Excellence and Trust in AI, Model Operations for Secure and Reliable AI, Unlocking the Value of AI in Business Applications with ModelOps, How ModelOps Helps You Execute Your AI Strategy, Implementing Predictive Maintenance Splunk. Expert Outlook: what will Facility Management be like in Industry 5.0? According to research conducted by Deloitte, a non-optimized maintenance strategy can reduce the production capacity of an industrial plant by 5 to 20%. Does predictive maintenance solve all ills? A few of these might include: While there are many benefits to predictive maintenance, there are also many disadvantages. Other possible problems that preventive maintenance could involve are related to the fact that, depending on the environment in which it operates, each machine works differently and the frequency of necessary maintenance could change. According to the RCM methodology (reliability-centered maintenance), the ideal is that 45-55% of maintenance is predictive, 25-35% preventive and only 10% reactive or corrective. As part of this stage, it is possible to detect anomalies, to train a classifier to identify different types of faults, to gain insights into what part of the machine, equipment or component need to be repaired, and to predict the trend the machine is likely to follow on its path to transition between the states. It is clear that unforeseen failures or problems cause temporal as well as considerable economic damage. Learn more about condition monitoring techniques, free demonstration with one of our specialists, 9 condition monitoring techniques that you must know.
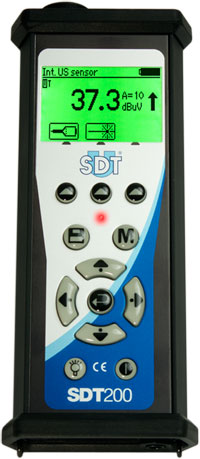
You might also like to read AI Act: A Risk-Based Policy Approach for Excellence and Trust in AI. Therefore, lets explain what predictive maintenance is in order to better understand it. You also want to make sure that you collect this data under different operating conditions. So how can we be sure that the models developed for our purposes can effectively perform within established thresholds? It is estimated that every single day, companies spend millions of dollars on data scientists, software engineers and artificial intelligence applications. Every maintenance manager would like to predict when a breakdown will occur. Implementing an operational framework for analytic models, including AI and ML, offers a number of benefits. Sounds like a nightmare, right? An example of an Enterprise ModelOps Platform can be seen in the following schema. In fact, research provided by the U.S. Department of Energy shows that predictive maintenance could result in a 30%-40% savings for the business that implements it. 2022 ONE SIX NINE INC. All rights reserved. This can be done also by using a failure data generator. While most businesses could technically use and benefit from predictive maintenance, there are a few specific industries for which the splurge is most worthwhile. Those who own or manage buildings can control and monitor buildings from any location using predictive maintenance technologyspecifically, software for ventilation and energy management. Infrared or thermal imaging tests (thermography). Some people may believe that predictive maintenance stops here. This monitoring can help improve overall energy costs for the building. Predictive maintenance requires a high capital investment in technology and labor to implement. Due to the fact that preventive maintenance only involves labor costs compared with the high initial capital investment on sensors, software, setup, and training that are indicative of predictive maintenance, preventive maintenance costs significantly less money to implement for your business. Predictive maintenance, also known as condition-based maintenance, is a proactive maintenance strategy that monitors the condition and performance of an asset in real time to predict when an asset needs maintenance before it breaks down. Thus, this predictive maintenance technique is. 400) ? Follow to join our 900K+ monthly readers, Giuliano Liguori is a technologist, an influencer in the digital transformation and artificial intelligence space. If a restaurants refrigerator were beginning to malfunction, or required any type of update, predictive maintenance technology could measure the functionality and alert restaurant staff to any issues. What has the equipment history been like thus far? No credit card required. This is an ever-growing market that is expected to be worth $225 billion by 2025. For example, the presence of silicone above 15 ppm can indicate that the insulation is wearing out, while sodium can reveal contamination with salt water. Types, Benefits, Cost, and Examples, What is Reactive Maintenance? ModelOps is important for predictive analytics at scale. To know more, schedule a free demonstration with one of our specialists. These are only a few facts and stats that reveal just how valuable a predictive maintenance program is, should the installation costs cover the approximate expenses of your broken machinery. Thats why. Since predictive maintenance is primarily executed by technological means (rather than manpower), its aim is to increase efficiency and productivity, as well as to reduce maintenance and equipment costs for businesses over time. Because preventive maintenance is done on a set schedule, it may lead to doing too much maintenance on an equipment. The advantage of infrared is that it allows you to make temperature maps, even from a distance. As this depends on obtaining quality data, the first step is to install sensors capable of collecting information in real-time on the performance and health of the equipment. For assets with low criticality, predictive maintenance may not offer great savings over the alternatives. Maintenance activities are then scheduled based on these forecasts. Maintenance planning can take 20-50% less time. Oil and gas industry often lack visibility into the condition of their equipment in remote offshore places. NDTs do not compromise equipment and can be performed while its running, just like routine check-ups for humans. inspection takes place after every 1,000 miles used). If you have already decided to invest in predictive maintenance in your company, recap the, The second step is to gather the necessary information to be able to transform the data you collected into actions.
when these parameters reach alarming levels. Not least important: it works on both AC and DC motors and can be used while the equipment is running. In the case of corrective maintenance, an object is used until a failure occurs. Preventive maintenance is the practice of systematically maintaining equipment, systems or machines in a manner that avoids or eliminates failures, or at least reduces their occurrence. Knowing at what stage a potential problem may arise is certainly within the capabilities of the machine manufacturer or whoever operates the machine. Investigate with the manufacturer the best way to integrate old models with new technologies. Blood tests, ultrasound scans, or eye exams: we do them every year, and none of them hurt us. However, as Artificial Intelligence becomes increasingly sophisticated, it is possible to detect anomalies even earlier, find correlations and receive intelligent suggestions to prevent a breakdown. We believe the factory, and the personnel responsible for its operations as well as the operation of the single machine must acquire the necessary skills in order to develop and manage AI for production. While predictive maintenance, tasks based on collected data and formulas, condition-based maintenance only. A study by the, in 2010, when installing sensors was even more expensive than now, points to. Using sensors and new technologies that monitor signs of deterioration and changes in the machines performance, managers can estimate when a failure will occur. The goal of preventive maintenance is to increase the reliability of a system while reducing the cost and downtime associated with failures. Traditionally there are two types of maintenance, corrective (or reactive) and preventive. Create your free account. We already mentioned that the cost of implementation is high, but even so, predictive maintenance has a high ROI, which can be up to 10 times the investment. Follow a metal guide (page 71) when using the spectrometer. The next step is to set up an optimization function that will be used for training and testing the model. Different particles reveal different damages to different components. Its not so much a question of if as it is when. Accumulating data about your assets is of no use if you dont know how to exploit them. Predictive maintenance is a field of computer science and engineering that uses data analytics to identify and predict equipment failures. Predictive maintenance also helps companies optimize their resources by scheduling preventive maintenance at times when it will have the least impact on production. In addition to analysing the circuit and its components, it evaluates the voltage and current entering the motor. Moreover, many businesses suffer from unexpected downtime due to equipment malfunctions each year. We already mentioned that the cost of implementation is high, but even so, predictive maintenance has a high ROI, which can be up to 10 times the investment. Infraspeak provides you with a multitude of apps, integrations and IoT hardware that will supercharge your team, business and maintenance operations. In addition, we must not forget that predictive maintenance requires a large infrastructure. The following macro stage is the identification of conditions, which allows us to train machine learning models that is the process at the heart of the predictive maintenance algorithm. Sensors would again come into play in this scenario to provide insight into assets using artificial intelligence. You might like to read also How ModelOps Helps You Execute Your AI Strategy. For example, the presence of silicone above 15 ppm can indicate that the insulation is wearing out, while sodium can reveal contamination with salt water. In a restaurant, the health of any food storage or cooking utility is paramount to the businesss success. The good news is that predictive maintenance lets you estimate time to failure. In new equipment, it is usually a simple process, but it can be more complicated in older machines. Different particles reveal many problems before you can guess a breakdown is coming. Even worse (depending on the scale of your business), one hour of downtime is worth approximately $250,000 of loss, with the average amount of downtime lasting around 4 hours. Corrective maintenance is the process of repairing or restoring equipment, system or machine to its original or working condition. NDTs do not compromise equipment and can be performed while its running, just like routine check-ups for humans. The major disadvantage is that it cannot be used on reflective surfaces. Artificial intelligence is able to process large amounts of complex data in a very short time, which is why many decisions are now delegated to machines. What do our records show regarding equipment downtime, defects, losses, and safety threats? More precisely, Enterprise ModelOps proves to be essential for large, complex enterprises with broad plans to leverage models across their operations, while ModelOps is required in some form by any organization. Here are some questions your business should consider before you decide to implement a predictive maintenance program: Implementing a predictive maintenance plan in your business requires that you first identify a list of critical assets for the programs implementation. In some cases, you may not have enough data to represent a healthy and faulty machine, so what you can do is build a mathematical model of the machine and estimate its parameters based on the sensor data. This technique is used, for example, in the maintenance of heating systems. on the performance and health of the equipment. But how? The most differentiating component of predictive maintenance is to build and apply algorithms that offer a prognosis. (in these cases, it is preferable to start with condition-based maintenance and gradually make the transition). As we have already seen, the idea is to predict when a breakdown will occur. This smart system would enable owners and managers to keep the building environment within a certain temperature range, track humidity, and more. In theory, it is easy to understand how predictive maintenance works. Predictive maintenance is often confused with condition-based maintenance, but there is an important nuance that distinguishes them. If you have already decided to invest in predictive maintenance in your company, recap the 4 steps you need to implement it: The first step is to identify the priority assets to include in the predictive maintenance strategy. One important aspect of this is that it enables manufacturers to build and deploy analytic models with any tool of their choice, automate ongoing monitoring, management, and governance of those models, regardless of where they are running, and integrate those models with the necessary systems and applications.